- 04.02.2022, 01:33
#560125
Hallo miteinander,
hier mal ein kleiner Beitrag über den Kauf eines OM 636 in der Hoffnung diesen ohne große Operationen verwenden zu können. Gekauft auf Ebay Kleinanzeigen, in einem für mich guten Zustand, der Motor soll in den 80igern überholt worden sein und hätte seitdem vorallendingen gestanden, man wisse nicht ob er laufen würde. Ein damals wohl neugekaufter Betriebsstundezähler wie auch Drosselklappe, 3 Wege Thermostat Gehäuse und Auspuffkrümmer ließen in meinen Augen darauf schließen das man bei der Überholung nicht verlegen war Geld auszugeben, für mich ein gutes Zeichen). Der Stundenzähler zeigte ganze 4 Stunden an was zu einem Probelauf passen würde.
So fuhr ich eines Tages ins Hannover`sche Umland und kaufte diesen Motor, der Besitzer war wohl ein "Pendant" aber leider schon verstorben.
Das ist der Patient, ach halt noch war er keiner.
Ich holte ihn nachhause und legte sofort Teile zurecht um den Einbau in einen Unimog realisieren zu können, beginnen wollte ich mit dem Tausch der Ölwanne.
Der Umbau hatte sich dann eigentlich schon erledigt, erheblicher Abrieb fiel auf
, da habe ich natürlich erstmal geschluckt. Aber solch einen Motor konnte man natürlich nicht wieder auf den Markt schmeißen und auch die sichtbare Konstitution ließ mich auf einen frisch überholten Motor schließen.
Also suchte ich zunächst nach der Ursache des Abriebs.
Hier die obere Lagerschale eines Pleuels.
Und der zugehörige Lagerzapfen
hier mal ein kleiner Beitrag über den Kauf eines OM 636 in der Hoffnung diesen ohne große Operationen verwenden zu können. Gekauft auf Ebay Kleinanzeigen, in einem für mich guten Zustand, der Motor soll in den 80igern überholt worden sein und hätte seitdem vorallendingen gestanden, man wisse nicht ob er laufen würde. Ein damals wohl neugekaufter Betriebsstundezähler wie auch Drosselklappe, 3 Wege Thermostat Gehäuse und Auspuffkrümmer ließen in meinen Augen darauf schließen das man bei der Überholung nicht verlegen war Geld auszugeben, für mich ein gutes Zeichen). Der Stundenzähler zeigte ganze 4 Stunden an was zu einem Probelauf passen würde.
So fuhr ich eines Tages ins Hannover`sche Umland und kaufte diesen Motor, der Besitzer war wohl ein "Pendant" aber leider schon verstorben.
Das ist der Patient, ach halt noch war er keiner.
Ich holte ihn nachhause und legte sofort Teile zurecht um den Einbau in einen Unimog realisieren zu können, beginnen wollte ich mit dem Tausch der Ölwanne.
Der Umbau hatte sich dann eigentlich schon erledigt, erheblicher Abrieb fiel auf

Also suchte ich zunächst nach der Ursache des Abriebs.
Hier die obere Lagerschale eines Pleuels.
Und der zugehörige Lagerzapfen
Viele liebe Grüße Hannes
_____________________________________________
Unimog 401 Froschauge der Berliner Stadtreinigung
Unimog 411.110 Patina forever
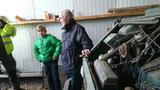
_____________________________________________
Unimog 401 Froschauge der Berliner Stadtreinigung
Unimog 411.110 Patina forever